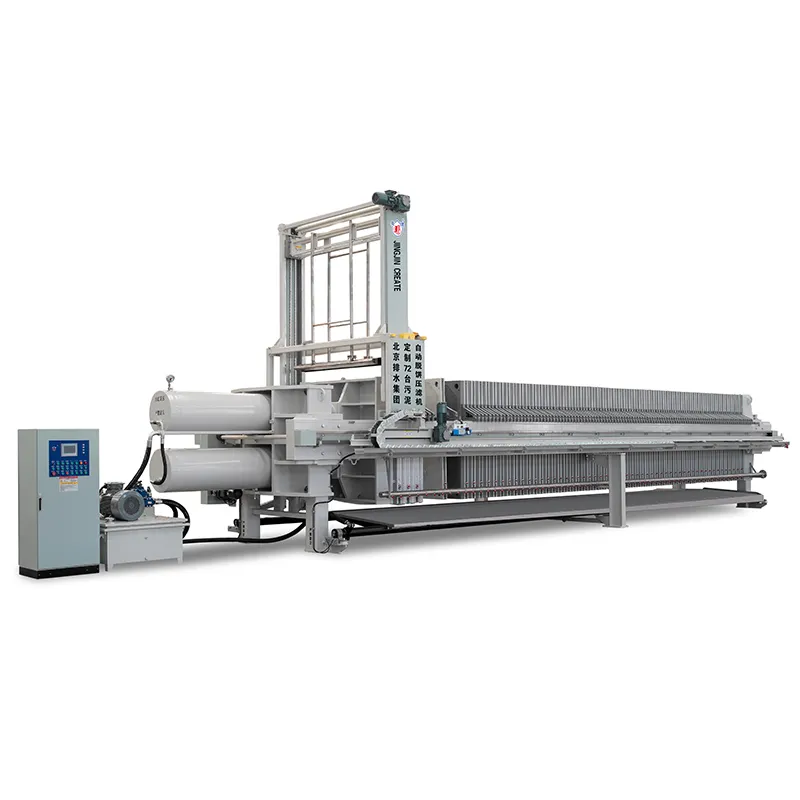
Charging stage: 1st, the mixture being handled (liquid containing reliable particles) is billed to the filter chamber of the filter press. The mixture passes through a uniform distribution around the filter fabric, forming a strong layer.
Chemical Production: In chemical plants, filter presses help in the recovery of treasured chemicals from waste streams and make certain compliance with environmental regulations.
Micronics layouts and manufactures industry-top filter presses in capacities from 2000mm x 2000mm (600 cubic ft) right down to purposeful, lab-scale filter presses like Micronics MicroPress with 150 mm filter plates.
All automatic filter presses are controlled as a result of an electro-hydraulic system, offering for a longer period life and lower running expenses than the hydraulic parts typically observed on filter presses. Controls could be tailored to offer complete automation for your personal current h2o treatment facility.
The filter pack is made of the filter plates stacked so as that make a hollowed chamber for solids selection. The major difference from the type of filter press is the variety of plates Utilized in the filter pack.
The vibrating device is useful for fully automatic emptying of filter presses and is also a steady further enhancement of your MSE Filterpressen® plate shifting system, which is referred to as robust. This system is made of:
A filter press is a versatile Device for strong-liquid separation, presenting productive and productive results across A variety of industries.
Our paddle dryers are engineered for maximum efficiency and longevity, guaranteeing they can take care of even one of the most demanding components. With our dryers, you are able to expect:
The control process of the PLC control system inside the automatic unloading filter press is as follows: Following the equipment is started off, the PLC gets alerts with the sensor, for example liquid stage alerts, pressure alerts, etcetera., to ascertain whether or not the equipment is in usual Operating problem; according to the preset process parameters and control logic, the PLC outputs control indicators for the actuator, which include commencing the Filter Press feed pump for filtering, driving the clamping mechanism for pressing, and so forth.
Fully automatic cross move systems for that filtration of wine and juices for big wineries and cooperatives
The automatic filter press and pump system control panel slowly enhances the pump pressure with the conventional unit to one hundred and five PSI. This permits for uniform filling of your filter chamber and steady cake good quality. This system frees up the filter press operator’s time for you to complete other duties.
Within this type, the filter plates Use a recessed chamber exactly where the slurry is pumped. The chamber permits a far more substantial accumulation of reliable cake, rendering it ideal for applications necessitating thicker cakes.
Soiled filter cloths or deposits on the reduced fringe of the filter plates are only some of the unwanted results. Very poor filtration effects and high mechanical hundreds for the fiter press are the consequences.}